With the progress of the investment casting process, not only the paraffin rosin-based low-temperature molding materials originally used, but also the paraffin resin-based multi-molding materials, and the trend of multi-variety and serialization. In particular, the development of the synthetic polymer industry provides a number of alternative additives for the synthesis of high performance model waxes.
The development of investment casting precision casting process is first made of wax, and then wrapped with a layer of clay and other refractory materials. The wax is melted and flowed out to obtain the empty shell formed by the refractory material, and then the metal is melted and poured into the air. The shell, after the metal is cooled, breaks the refractory material to obtain a metal mold. The process of processing the metal is called precision casting, which is also called investment casting or lost wax casting.
This method has been around for a long time. In the hundreds of years before BC, the ancient Chinese working people created this lost wax precision casting technology, which is used to precisely cast products such as Zhongding and utensils with various fine patterns and characters. . According to expert appraisal, the bronzeware of the Yin Shang period unearthed in China and the Zeng Houyi tomb of the Spring and Autumn Period were used in the manufacture of such a clever technique. The base of Zenghou Yi's tomb is a pair of intertwined dragons, connected end to end, staggered up and down, forming a multi-layered cloud pattern in the middle hollow. These patterns are difficult to manufacture by ordinary precision casting process, and the lost casting wax precision casting process can take advantage of the fact that paraffin has no strength and is easy to engrave, and can be engraved with ordinary tools to be the same as the tomb of Zenghou Yi. The paraffin-made crafts, and then the additional pouring system, paint, dewaxing, pouring, you can get the exquisite Zenghou Yi tomb. In the manufacture of metal jewellery and many non-metallic handicrafts, the use of this method has a long history and is still the main method for the production of many jewellery and handicrafts.
Modern investment casting is based on the ancient wax mold precision casting. During World War II, the allied technical experts in Baoshan, Yunnan Province, were deeply inspired by the local people to make crafts in this way, and they were improved and used in the production of mechanical components. Since then, this technology has been rapidly developed around the world. The practical application of modern investment casting methods in industrial production was in the 1940s. At that time, the development of aviation jet engines required the manufacture of heat-resistant alloy parts such as blades, impellers, nozzles, and the like, which were complex in shape, accurate in size, and smooth in surface. Since the heat-resistant alloy material is difficult to be machined and the shape of the part is so complicated that it cannot be or is difficult to manufacture by other methods, it is necessary to find a new precision molding process, so it is based on the lost wax casting that has been handed down from ancient times, after the materials and processes. Improvements, modern investment casting precision casting methods have achieved important development on the basis of ancient techniques. The development of the aviation industry has promoted the application of investment casting, and the continuous improvement and perfection of investment casting has created favorable conditions for the aviation industry to further improve its performance. Since then, this advanced precision casting process has been greatly developed and has been widely used in the manufacturing industries of aviation, automobiles, machine tools, ships, internal combustion engines, gas turbines, telecommunications equipment, weapons, medical equipment and cutting tools, and also used in the manufacturing industry. Manufacturing of arts and crafts. In the past decade, investment casting has been moving forward at a relatively high speed. The world's major industrial countries are increasing at an average rate of 7% to 12%, and special-purpose castings will increase at an alarming rate of 30%, thus promoting the development of investment casting precision wax development technology.
Development of wax for investment casting Precision casting wax is a special material for manufacturing part molds in investment casting, and is one of the important factors determining the quality of castings. The wax varieties for investment casting mainly include low temperature molding materials, medium temperature molding materials and high temperature molding materials. At present, the main molding materials used are low temperature molding materials and medium temperature molding materials. The molding materials imported from China are also mainly medium temperature molding materials. The United States has a high level of investment casting technology, benefiting from three pillars, namely advanced technology, high-quality raw materials and strict and serious operations. For example, the mold materials used in the US investment foundry are new mold materials produced by the mold factory. The investment foundry does not recycle the used mold materials, and the recovered mold materials are sent to the professional production plant for processing. Due to the high quality and uniformity of the mold material from the mold factory, the dimensional accuracy and surface quality of the wax mold of the investment foundry are guaranteed, and the ash and impurities of the wax are also controlled. Foreign companies usually have professional companies that bring together relevant technology to produce investment casting molds. The molded material produced has good stability, low shrinkage, smooth surface, high strength, good formability and production of different properties for different parts. The types of molding materials produced abroad include filler molding materials and non-filling molding materials, and are subdivided into model waxes, repair waxes, emulsifiable waxes, gate waxes, and waxes for sealing waxes.
In recent years, many units in China have successfully developed many series of mold materials and the quality of the products is high. China's Beijing Zhengda De Technology Development Center has developed and produced WMII series of molding materials. This series of molds can be used to replace imported products by providing mold materials for different shell materials, different dewaxing temperatures and different size shapes. Shanghai Jinshan Mould Material Factory produces WM series mold materials, more than ten varieties, with an annual output of about 200 tons. Shenyang Foundry Research Institute develops and produces medium temperature molding materials and filler molding materials such as F-01. In addition, Shenyang Fengdong Tools Factory, Beijing Oil Pump Nozzle Factory, Taiyuan Jinxi Machinery Factory and Chengdu Chemical Industry Institute also produce high quality wax-based medium temperature molding materials.
The production of foreign investment casting wax mainly includes CL-162 series and Master series mold materials produced in the United States, Castylene series mold materials produced by Dussek Campbell Company of the United Kingdom, K series mold materials produced in Japan (such as K512) and production in the former Soviet Union. P-3 moldings, etc.
The performance of the mold material is determined by its formulation, so each manufacturer pays great attention to the study of the mold formula.
Domestic precision casting wax consumption status and market forecast China began to apply investment casting in industrial production in the 1950s and 1960s. Compared with foreign countries, the domestic investment casting precision casting industry is relatively early, but the development of precision casting wax for molding materials is relatively lagging behind. Before the 1990s, most of China's investment mold manufacturers used paraffin stearic acid mold materials and water glass shell molds to produce investment castings with low quality requirements. Before 2006, there were about 1,350 such precision casting factories in the country, with an annual output of 150,000 tons of castings, and about 3,750 tons of precision casting wax containing paraffin stearic acid as the main component.
In 2007, the amount of precision casting wax in some parts of China was as follows.
Northwest China: The amount of low-temperature precision casting wax in Ningxia and Xi'an is about 500-800 tons/year, and the medium-temperature precision casting wax is 100-200 tons/year. Among them, Ningxia Wuzhong Instrument Factory and Xi'an Aero Engine Co., Ltd. low-temperature precision casting wax self-modulation, medium-temperature precision casting wax mainly depends on imports.
East China: The market for low-temperature precision casting wax is relatively large, in the range of 1000-2000 tons/year, and the medium-temperature precision casting wax is about 100-300 tons/year. It is mainly used for processing castings abroad, and casting wax is more in Taiwan.
Zhongyuan area: There are few investment casting enterprises, mainly low-temperature precision casting wax, mostly self-adjusting products, Luoyang No. 1 tractor plant dosage more than 100 tons / year.
In addition to other regions, the domestic market capacity of precision casting wax reaches 5,000 tons/year.
The mold used in most of China's investment casting foundries is the paraffin wax, a low-temperature molding of stearic acid. Its low quality, high cost, and seriously affect the improvement of casting quality, the castings produced are less competitive in the international market. However, many investment casting factories in China hope to produce castings for export. When castings are to be exported, it is necessary to improve the quality of casting products. Therefore, on the one hand, advanced investment casting equipment is required, and on the other hand, high quality molding materials are required. Obviously, the self-sufficient mold production method of the investment casting factory is difficult to produce high-quality mold materials, and this situation is in contradiction with the modern large-scale production. In recent years, China has introduced many modern investment casting equipment and high-quality molding materials, and with the increasing exchanges with overseas countries, the variety and specifications of imported molding materials are increasing. It can be seen that the production of mold materials in China faces the arduous tasks and challenges of improving the quality of mold materials and expanding the variety of mold materials.
Conclusion With the progress of the investment casting process, not only from the initial use of paraffin rosin-based low-temperature molding materials to paraffin resin-based multi-molding materials, but also a variety of varieties, serialization trend. In particular, the development of the synthetic polymer industry provides a number of alternative additives for the synthesis of high performance model waxes. However, due to traditional habits and considerations of product tolerances and cost factors, many manufacturers using cast waxes maintain the original supplier (importer) as much as possible, and dare not easily replace the wax material. Therefore, in the market, you can see the model wax material with advanced performance, and you can also see the case where the natural animal and plant wax is still used as the casting wax. The variety of wax materials is varied. Some manufacturers are rough and arbitrarily, and do not consider the application and use effect of the products at all. Some of the foundry manufacturers do not have high requirements for the model wax, and simply formulate the wax materials themselves, so that the defective rate of the terminal products remains high. It is believed that over time, model wax materials with relatively poor performance will be phased out, and market chaos will be improved.
Http://news.chinawj.com.cn Editor: (Hardware Business Network Information Center) http://news.chinawj.com.cn
Calcium Chloride Description :
Calcium chloride is an inorganic salt, which exists as solid or liquid. Solid calcium chloride is a white, crystal substance in the form of flake, granule, pellet or powder. With different crystallized water contents, it can be dihydrate or anhydrous. Liquid calcium chloride is a colorless, clear solution. As calcium chloride has such properties as quick dissolving, exothermic ability, attracting moisture from the air and surroundings, dissolving at very low temperature
Calcium Chloride Application :
1. They are widely used in highway, expressway, parking lot and port to melting snow and ice.
2. Used as dryer, as anti-fog, and anti-dust agent also fireproof agent
3. Protective agent and refining agent for petroleum/oil field.
4. Pigment assistance agent of textile. It is a kind of raw material.
5. It acts as flocculation in water treatment.
6. Be used in waste paper processing as removing printing ink agent.
7. As anti-freezing agent.
8. As dehydration agent.
9. Food additive: as cryogen are used in ice cream, as stable agent/coagulant used in bean products, drink and beer.
94% calcium chloride pellet
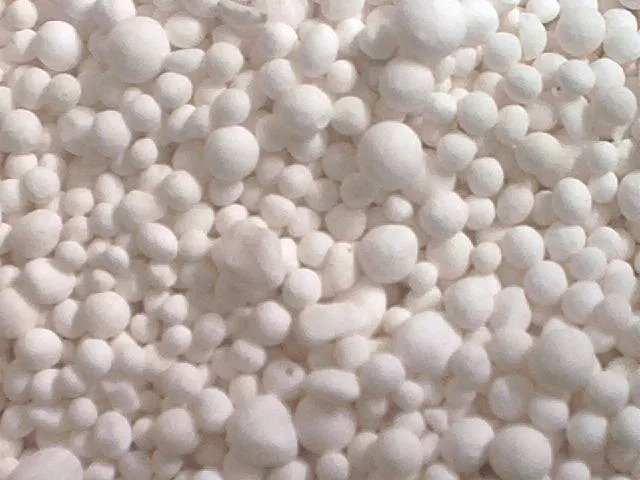
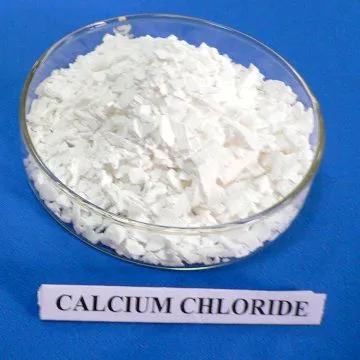
Calcium Chloride Specification
Item |
Standard |
|
74% Flakes/Granular |
77% Flakes/Granular |
|
Calcium chloride as CaCl2 |
≥74% |
≥77% |
Total alkali chloride as NaCl |
≤7.0% |
≤5.0% |
Total magnesium as Mgci2 |
≤0.5% |
≤0.5% |
Alkalinity as Ca(OH)2 |
≤0.4% |
≤0.4% |
Insoluble in water |
≤0.3% |
≤0.2% |
Item |
Standard |
|
94% Prills |
94% Powder |
|
Calcium chloride |
≥94.0% | ≥94.0% |
Magnesium and alkali chloride(NaCl) |
≤5.5% | ≤3.5% |
Water insolubles |
≤0.2% | ≤0.2% |
Alkalinity[Ca(OH)2] |
≤0.35% | ≤0.3% |
Sulfate(CaSO4) |
≤0.2% |
≤0.2% |
FE |
≤0.1% |
≤0.1% |
Calcium Chloride Package
25KG/ 1000KG PP woven bag
Calcium Chloride
Calcium Chloride,Calcium Chloride Flakes,Calcium Chloride Pellets,Calcium Chloride Dihydrate
Shandong Tiancheng Chemical Co., Ltd. , https://www.akdchemical.nl