Before 2010, China was the largest production base of Nike, but since then it has replaced the position of China. In 2001, China produced 40% of Nike's shoes, while Vietnam only produced 13%; by 2005, China's share fell to 36%, Vietnam rose to 26%; in 2009, the two countries tied for a 36% share; In 2010, Vietnam rose to 37%, eventually surpassing China's 34%.
This seems to portray a clear trajectory of the fall of China's manufacturing industry.
To understand the inner logic of this trajectory, we must dispel the fog and dig up the foundry giant behind the scenes. The company, called Baocheng Group, is the world's largest shoe-making foundry. Last year, it produced 317 million pairs of shoes. One pair of five pairs of sports shoes in the world was shipped from the Baocheng factory. After deducting the walled goods, basically the vast majority of Nike, Adidas, Converse, New Balance, are derived from here.
At present, Baocheng has 410,000 employees and is located in three major factories in China, Vietnam and Indonesia. In terms of production share, the proportion of China in 2015 is already the smallest of the three major factories, leaving only about half of Vietnam.
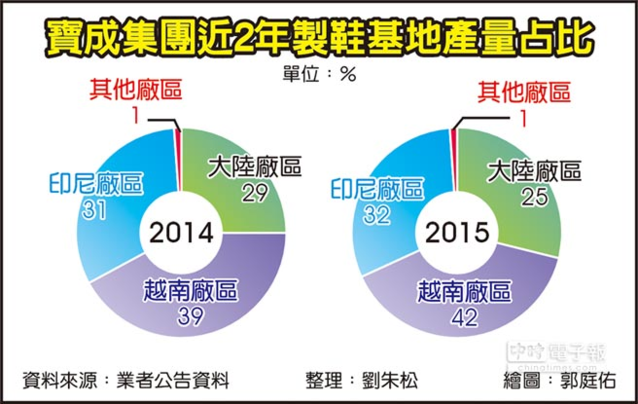
In 1969, the company was born in the Lukang town of Taiwan. At the beginning, it was only a small workshop for the production of rain boots and slippers. In the decades since he grew up, he has been facing the brutal competition of his peers and the impact of Korean shoemakers. The development is quite rough.
In the end, it will stand out from the crowd and have a close relationship with Bao Cheng’s boss Cai Qirui’s decision. In the mid-1980s, the New Taiwan dollar and the Korean won began to appreciate at the same time, forcing the footwear industry to leave. At that time, because South Korea did not establish diplomatic relations with China, Korean companies could only go to Indonesia to develop, while Cai Qirui chose to enter the mainland, and built a modern factory of 10,000 people in Zhuhai and Dongguan.
This decision made Baocheng's labor cost drop sharply, and orders were like snow flakes, which laid the foundation for hegemony. His main competitor, who was not adapted to Indonesia's culture and management style, was eventually tossed to death.
For Baocheng, the mainland is the feng shui treasure land of the rise of the family. It is not forced to leave.
However, Baocheng, still left, took his tens of billions of orders every year and went to Southeast Asia.
There are two reasons for Baocheng to finally make up his mind to leave. The first is the cost of transportation. If China's inland land does not depend on the sea, if it is transported by land, the cost will be much higher, and the value of the shoes will be very low. The ex-factory price of a pair will be tens of dollars, if the logistics cost is high. The business can't do it anymore.
The second is labor costs. The footwear industry is very sensitive to payroll expenses. Let's look at the economic comparison between China and Southeast Asia. By 2015, the per capita GDP of China's coastal areas has reached 10,000 US dollars. Even in the central and western regions, it has generally risen to 5,000 to 6,000 US dollars, while Vietnam in Southeast Asia has only 2,000 US dollars in the same period, which is about three in the interior of China. About one point.
This huge gap in GDP per capita has a decisive impact on the cost of wages. Coupled with the high cost of transportation, Baocheng has no way to resist it, and can only follow the trend of the tide. Their fourth production base has been built in Myanmar, where the per capita GDP is only $1,000, half that of Vietnam.
Among the Taiwanese businessmen who came to the mainland in the same year, there was a man named Guo Taiming who often went to the factory in his hometown to study.
Baocheng's vertical industrial chain integration technology is very good. His upstream suppliers of shoe materials have more than 100 enterprises. If you are not careful, it may cause accumulation of raw materials. However, the computer automation management system that he introduced earlier made the response between the various component suppliers very timely, the inventory preparation time was greatly reduced, and the capital turnover efficiency was improved.
On the other hand, Baocheng has developed from the simple OEM OEM model to the ODM model of “OEM + Designâ€, which has opened up the eyes of Guo Taiming. He copied these experiences to his electronics factory and soon rose to IT. A giant in the field of manufacturing.
In 2002, Foxconn, a subsidiary of Guo Taiming, jumped to the top of China's export manufacturing industry and has been in the list for more than a decade.
Bao Cheng left, but Foxconn chose to stay. His factory went all the way west, moved out of Shenzhen, and moved to Chongqing, Chengdu, Wuhan, Zhengzhou, Taiyuan, and Heze. Foxconn's factories can be found in almost every province in the central and western regions. In 2015, Foxconn had 1.2 million employees in China with an export value of 120 billion US dollars, accounting for one-twentieth of China's total exports.
This is a very amazing number. Why did Baocheng go, but Foxconn did not go? Although the IT manufacturing industry is also a labor-intensive industry, several key features have led them to part with the footwear industry.
First, the value of the IT industry is relatively higher. The ex-factory price of a pair of shoes is usually only tens of dollars, but a mobile phone must be at least a few hundred dollars. This makes them able to withstand the pressure of land transportation costs. If it is a luxury item such as Iphone, it is also assumed to be transported by airplane. This is the reason why Iphone production is arranged in Zhengzhou, where it is important inland. Transportation center.
Second, advances in industrial robot technology have made IT manufacturing a beneficiary, and the proportion of compensation costs in total costs has begun to decrease. Robot technology has not been accurate enough in the past, so it can only be used in heavy industries such as automobiles. However, in recent years, with the advancement of sensor technology and software technology, many types of work on the electronic assembly line can be completed by robots. For example, Foxconn's Kunshan factory has reduced the number of workers by half in the past five years.
Third, the technological innovation of shoes is slow, and the development space is limited, but the progress of IT technology is changing with each passing day, and you always have the opportunity to grab the vent. Foxconn's latest stop in the interior is Guizhou, where it will be built into a large data center, and a 6-generation LTPS (low temperature polysilicon) panel factory will be built with an investment of 25 billion yuan. The partner is Huawei. These businesses are not tried by Foxconn before, and the profit margin is higher. For emerging businesses, the market size is more important than the compression cost.
Although it has been rumored to leave China, Foxconn has not really stepped out of this step.
Up to now, more than 80% of Foxconn's factories are located in the inland areas of China. Although the wage costs here have been increasing, the advancement of technology and the continuous upgrading of the industry have made Foxconn have the confidence to stay.
This spring, Foxconn acquired Sharp, a century-old store, in order to acquire its advanced screen manufacturing technology. Sharp is one of the screen suppliers of Apple's iPhone. After the completion of the acquisition, Sharp's Japanese factory will be laid off, screen manufacturing technology will be introduced to China, to Zhengzhou, or Guizhou factory to produce, all within the planning.
The transfer of Chinese manufacturing to Southeast Asia is currently only the lowest-end textile footwear industry, and industries with higher technology content and better profit margins are continuing to move westward in an orderly manner. For example, the high-generation panel industry, including AMOLED screen and LTPS screen, has six production lines under construction in China in 2015. The production capacity in 2016 will be expanded by 210%, such as the Chengdu plant of BOE, the Wuhan plant of Huaxing Optoelectronics, and the Wuhan of Shentianma. And the Xiamen plant, Foxconn's Zhengzhou and Guizhou factories, will be put into production in the next year or two.
This wave of investment is one of the signs of China's manufacturing upgrade. They invest in technology and the future. After all, it has the largest single market in the world, social stability, and talent-intensive, far from being comparable in Southeast Asia.
Spray Grain Texture Pu Sandwich Panels
Rich selection of textures and colors meet different decoration requirements, giving the city and the buildings a new look.
The PU foam is the most advanced and eco-friendly insulation material in the world. With the help of the back aluminum foil, the thermal preservation effect achieves the best.
The unique structure prevents the heat loss in winter. Meanwhile it reduces the heat of the summer sunshine.
Aceta paintcoat and flurocarbon paint of weather resistance performance are applied on surface of wall panel. It is reserved with superior self-cleaning, weather resistance, corrosion resistance and acid& alkali resistance performance.
Light weight with 3.7Kgs/m2 makes the installation easy.
The installation process is clean and tidy without any noise and dust, construction waste.
Different selections of accessories meet different effects.
High quality and stable performance: Manufactured in CNC automation production line, the product pass rate can reach 99.9% with stable chemical structure and physical structure.
Spray Grain Texture PU Sandwich Panels
Metal Cladding Panels,Insulation Metal Cladding Panels,Spray Grain Texture Pu Sandwich Panels,Spray Grain Texture Pu Sandwich Panels
Jinan Zhengtang Insulation Decoration Material Co.Ltd , https://www.ztwallsiding.com