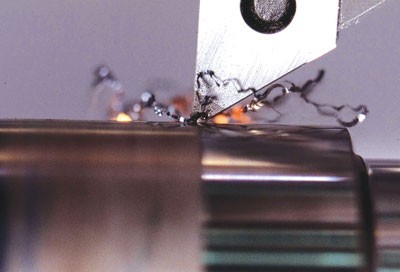
Figure 1 Advanced cutting tools can increase the efficiency of the shop.
Tool technology is rapidly evolving to meet changing needs and address the toughest challenges from workpiece materials. Today's processing plants need to revisit the tool from different perspectives. In the case of meeting various needs, the use of advanced tools can improve the processing capacity of the workshop. The figure shows the tools for turning hard materials. Tool technology is evolving rapidly, so choosing the right tool can make a fundamental shift in the process. In the metalworking industry, there is no alternative to advanced technology. In the future, the demand for machining will be very large, and only advanced technology can meet this huge demand. Take the aerospace industry as an example: In the next 20 years, in order to meet the production needs of the aerospace industry, its production and processing capacity must be tripled from now on. So how do you achieve this goal? Is it possible to triple the processing capacity by three times, is it simple to triple the number of machine tools, and the processing technology still maintains the current level? Today, he said, it is impossible to actually Case. If you multiply the number of machines of the state of the art by 3, it means that the number of machine operators will increase by the same factor. This situation is simply unimaginable, because it is quite difficult for the factory to hire qualified workers who are qualified for the operation of the processing machinery. Therefore, three times the production capacity needs to be obtained from the evolving advanced technology, and only in this way can the existing number of metal processing operators monitor a large number of machining operations. So where do these advanced technologies come from? Of course, these technologies also involve the development of the machine itself. Nowadays, the machining speed and machining accuracy of machine tools are getting higher and higher. However, the workpieces themselves are not developed in the same incremental order, although they are also undergoing substantial changes. Nowadays, the processed workpieces not only put forward higher requirements on the processing precision, delivery time and quality, but many workshops are faced with more and more difficult materials that have never been encountered before. These materials include titanium alloys, nickel-based alloys, and compact graphite cast iron (CGI), not to mention, in some cases, composite materials instead of metal materials. In other words, the development of workpiece materials is faster and more varied than the machine tools that machine them. There is a certain gap between the machine tool and the part material. In order to reduce or even exceed this gap, the fastest-growing technology comes from metal cutting tools, and its development speed exceeds that of any other processing technology. It turns out that the development and changes of the tool are so great that, regardless of the size of the processing plant, it is necessary to re-evaluate the processing ideas of the tool. Not only does it need to re-examine the tool selection method, but it also needs to rethink some of the basic factors that affect the tool. But some of the core ideas are outdated and the standards for tools have changed. Recently, three major companies related to knives have suggested how the processing shop should now think about the knives in different ways. These companies are: Diamond Innovations, Inc., the world's leading supplier of cubic boron nitride (CBN) materials and polycrystalline diamond (PCD) materials for tools; Precision Dormer, the alliance of two tool companies, dozens of companies Specialized technology for high efficiency drilling and threading has been available for the past year; Sandvik Coromant, the world's first supplier of metalworking tools. All the engineers and technicians of the three companies listed some of the main factors that currently have a fundamental impact on the nature and use of the tool: Challenging materials, including alternative materials and difficult-to-machine alloy materials. Some of these materials are less than 25% more steel, and can cost hundreds of dollars per pound of processing; parts with increasingly complex geometries, such as aircraft parts with very thin walls and complex shapes; The demand for parts, especially for turbines and various heavy equipment, continues to increase. The high-cost production of each part places more stringent requirements on the processing of these parts; the requirements for specialized quality and performance are increasing, such as the typical fatigue strength requirements for the surface of machined parts. All of these factors have prompted those leading processors to start thinking about the relevant tooling issues. Diamond Innovations, Precision Dormer and Sandvik Coromant have proposed five ways in which the shop must think differently about their tooling techniques and the companies that offer the technology. The five new criteria for selecting tools are: improving machine tool efficiency, meeting application expertise, increasing the percentage of diamond tool applications, focusing on the largest cost source, and considering tool issues from the start. Improve machine productivity Don't just choose tools that have a longer life or higher speed. Innovative tools can also change the process and expand the machine's processing range. The CoroTurn HP tool focuses on the flow of high pressure coolant, with the coolant injection point concentrated above the cutting edge. Practice has shown that using this method to spray coolant can increase tool life by 50% and speed by 20%. Why do machine shops choose to change tools under normal use? The most common reason is that they want to extend the life of the tool. If the new tool can work longer in the existing process, it can save more money for the shop, including replacement tool costs and labor costs for multiple tool changes. In order to increase the speed of machine tools, many innovative machine shops will try to use new tools. If the new tool plays a very good role in the high-speed machining process and greatly improves the metal removal rate, the tool can save more money for the workshop. In other words, the tool can increase the productivity of the shop more efficiently, allowing it to process more parts per shift. These two major improvements in the process – the increase in service life and processing speed – indicate a return on investment, which also makes many shop floors more reason to use high-performance tools. However, the quest to improve the craft level through the tool should not stop here, it also has great potential to save more money. Therefore, the processing shop should try every means to find ways to improve their processing capabilities, because advanced tools can not only extend the processing technology, but also promote the process to further improve. In many of today's hole processing applications, there is no longer a need for reaming. Drilling can achieve higher quality standards than ever before, giving the shop a greater potential. To achieve this, the necessary hole machining accuracy can be achieved by drilling this process. Quality requirements. In many processing plants, although the hole machining process using center drills, drill bits and reamers may be very familiar, it is difficult to overlook the cost of this process. If the change in the cutting parameters of the drill is roughly equivalent to the parameters already in use in the shop, then a hole of the quality can be machined. Even if the price of the new tool is slightly higher, the added cost can be said to be negligible compared to the cost savings, because no unnecessary tools are needed in the machining process, thus eliminating and solving the machining. Tool replacement problems not required during the cycle. In fact, there are many ways to increase productivity through the development of tools. So the workshop needs to think about how to use the tool correctly to take advantage of its potential. 1. Using the characteristics of the machine tool Is your tool capable of exerting its full potential so that the machine tool can improve the machining level every day? Generally, in the processing of machine tools, the most popular is the use of high-pressure coolant. At present, there are very few processing workshops that allow their tools to fully utilize 70 bar (1 bar = 0.1 MPa) pressure coolant for machine tools. CoroTurn HP tools can be used to increase the efficiency of the high-pressure coolant precisely onto the blade directly above the tool. The CoroTurn HP tool holder converts the high-pressure cooling flow into a wedge shape, which causes the chips to warp upwards and is cut by the cutting fluid. go. In the processing of difficult-to-machine materials, Inconel 718, this method can be used to increase tool life by 50% or increase speed by 20%. 2. Reduce installation time The Coromant Capto system is the industry standard for fast tool change systems in turning. It allows quick tool change or quick tooling of new workpiece machining tools without the need to adjust tool position or reset tool offset. The same Coromant Capto concept has also been applied to rotary tools, which makes the use or replacement of new milling tools or drills extremely convenient, and the locking position is fast and does not extend any replacement time.
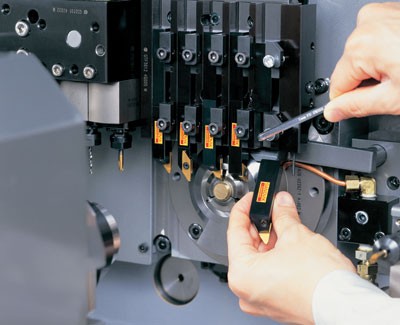
Figure 2. After using the QS system on a Swiss-style lathe, the positioning can be quickly and automatically locked. A company that uses Swiss-style lathes saves a lot of tool commissioning and installation time each year and saves $100,000. 3. Using the QS system QS system is another system that reduces installation time. On Swiss-style lathes. With the QS system, the tool can be quickly loaded and unloaded and automatically locked in position on the center. According to the calculations of a shop floor user using a Swiss-type lathe, the system can save $100,000 per year in the commissioning and setup time of a machine (Figure 2). Adopt unmanned management mode of operation. In addition to the tool life and speed, you should also think about the reliability of the tool. At present, no workshop can fully understand the potential value of the tool, and it is not known how high the tool can reach the constant performance level. Why is constant performance so valuable? Because it can change the process with the highest potential profit, enough to free the operator from machine operation, enabling it to operate more machines, inspect parts, or run on machine tools. Simultaneous implementation of related 5S technology or other lean production management work. If the machine shop can accurately predict when the tool needs to be replaced, the shop can run its machining process in this way, without having to ensure that an operator stays at the job site. The new GC1125 and GC1515 grades are specifically designed for "green light production". The reliability of the insert comes from the balance of the coating and the matrix material. In order to improve the toughness and density of the tool, the hardness of the matrix material is slightly lower, and the composition of the coating is beneficial to improve the wear resistance of the tool. The cutting edges of these tools are also very sharp, which is another important feature of the “green production†tool. Because the sharp edge helps to eliminate burrs, the function of automatic burr removal is very important for long-term unmanned operation, because the workshop runs in this way, and it is not expected that large parts will be processed after completion. A lot of deburring work is also required.
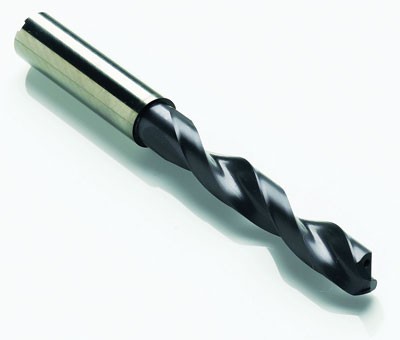
Figure 3 shows another tool designed to process specialty materials. In stainless steel machining, the drill uses a small machining allowance to minimize contact with the workpiece surface and to avoid work hardening of the stainless steel workpiece surface. The effective geometry and coolant input holes further help solve the problem of chip breakage and discharge in stainless steel machining. Meeting the needs of application expertise If the choice of tool technology is expanded, the key components of a tool need to have dedicated technical support behind it. When developing high-performance tools, tool companies typically design tools and tooling systems to achieve the high performance required for specific machining applications. Tool suppliers often develop tools for a wide range of special applications, resulting in an ever-increasing range of tools and tools. In fact, today's processing plants can't rely on their limited knowledge to decide how to use the right tools, but to find a professional tool supplier. The body of the technical expertise is available in several different forms, including: 1. Professional research on materials. Various methods of designing drill bits according to performance requirements. In the past, the requirements for tools were only “coated†or “coatedâ€, and now a variety of different coating materials have emerged to meet the needs of different materials. Nowadays people pay more attention to matrix materials, which is the most important area of ​​tool research and development today. Second, the geometry of the tool itself is also important. These factors are mainly for the tool, not just for materials that are difficult to machine. Taking aluminum alloy materials as an example, the tungsten content is extremely high in tools specially designed for aluminum alloy processing. The surface of the workpiece machined with this tool is of good quality and prevents the blade from curling. In addition, its geometrical angle allows the chips to straighten and break, preventing the aluminum from becoming soft and sticky. Careful consideration of similar issues ensures that the drill bit achieves its highest performance in the processing of any metallic or non-metallic material. 2. Understanding the workpiece In addition, the geometry of the workpiece also has great significance for the selection of the tool. Complex workpieces place a heavy burden on the shop's investment in non-standard tools, because challenging gap problems must be solved, and non-efficient tools may result in insufficient cutting force and insufficient support, making it difficult to handle materials with lower hardness. . A professional tool supplier should not only have professional research in materials, but also have processing systems specially designed for "difficult" workpieces in the processing of such parts.
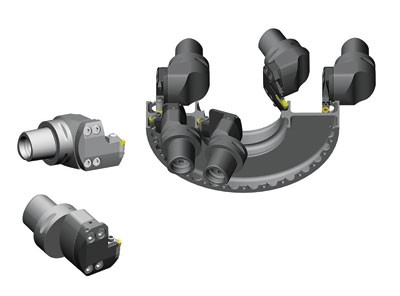
Figure 4 The SL70/40 system provides stable re-cutting of turbine blades and turbine casings. It requires only a few different configurations of modules to allow the tools to be properly clamped and positioned, and provides examples of suitable machining gaps for various turbine machining operations. Turbine blades and turbine casings are such "difficult" workpieces. These complex turning parts are often made of difficult-to-machine alloy materials, generally with molded crypts, and require tools to meet various difficult clearance requirements. To overcome these difficulties, the modular SL70/40 tooling system, a freely configurable quick-change system, is suitable for the stable machining of heavy-duty parts such as turbine blades and turbine casings (Fig. 4). This tooling system requires only a few modules and different configurations to ensure proper machining of the various turbine workpieces with the right clearance. At the same time, HP technology integrated into this tool can be sprayed directly over the cutting edge. High-pressure coolant to help solve the processing problems of difficult-to-machine materials. 3. Cognition of the end market Different industries also have different processing requirements, and tool suppliers should be able to help the shop meet these requirements. Certain materials themselves are also increasingly changing with specific industry requirements. Composite materials are a good example. The challenges faced by certain machined parts are also related to certain industries. This is an important issue to consider, and few processing shops outside the aerospace industry will face such problems in the same way. However, in the aerospace industry, processing forces and temperatures produce microhardness changes, plastic deformations, and residual stresses that cause parts to be less accurate. Tool and cutting technology was developed to control the wear of this edge in some way, and this method even allowed aircraft part producers to meet most of the required surface integrity requirements.
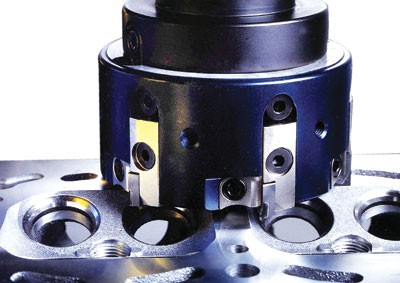
Figure 5. There is a certain relationship between more advanced workpieces and more advanced tools. The emergence of diamond tools also increases the need for efficient machining of aluminum alloys. The percentage of diamond tool applications can increase the efficiency of machine tools. Provide professional solutions to meet more demanding applications. In any case, as long as the production capacity is tight, you should consider the application of polycrystalline diamond (PCD) or cubic boron nitride (CBN) tools. There is a direct connection between advanced workpieces and advanced tools. As with automakers, more and more high-performance materials are being used for demanding parts. In order to process these materials in the most efficient manner, the use of diamond tools is becoming more common. This is also the case in the aircraft manufacturing industry, where they are increasingly using diamond tools to meet the growing demand for titanium machining. Another important area of ​​application for diamond tools is the machining of composite materials, as long as the machine itself is suitable for diamond tooling. Precision Dormer has designed and developed a range of drill bits, such as drill bits with carbide hard materials, diamond coatings and PCD materials, to apply different grades of processing equipment to drill different apertures on composite materials. Diamond tools and diamond-like tools, whether PCD, CBN or diamond-coated tools, will increasingly enter processing applications. Moreover, the proportion of tools used in this type of material will continue to grow.
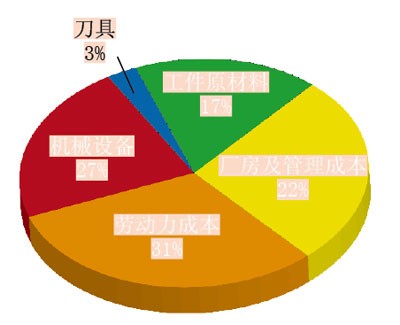
Figure 6 shows the source of the cost of a typical workpiece from the pie chart. The table converts the percentage of each cost into dollars and cents. Because machining and labor costs are so large, faster cutting can provide a great opportunity to save a lot of money, even as the cost of cutting tools increases. This is an inevitable development trend. The development of PCD and CBN materials has led to an increasing use of these materials, making the variety of tools more colorful and cost-effective. At the same time, the machining speed and service life of these tools continue to increase, making the machining process reach the level of performance never reached by carbide carbide tools. In fact, diamonds and their associated tools meet the aforementioned “improving the productivity of machine tools†and “meeting the needs of application expertiseâ€. Due to the extended service life of the tool and improved cutting parameters, the tool's machining capability is improved, the frequency of tool change is reduced, and the machine can process the production parts at a higher speed. At the same time, more professional technical solutions are integrated into the tool to further meet the needs of various application fields. 1. Processing of high-performance parts In the production of auto parts, the development of automotive engines to higher performance has also promoted the development of materials in a more difficult process. For example, valve seats for intake and exhaust valves are increasingly made of special alloys. Other engine parts are also beginning to use high density graphite cast iron (CGI). The demand for ever-increasing cast iron parts has also had a major impact, as new cast irons are more difficult to machine than aging-treated cast iron. Practice has proved that the use of CBN tools is the best solution for such challenges in the automotive industry. However, in the aerospace industry, the use of complex tools may be an excellent opportunity to increase productivity. The new aircraft design will place higher demands on titanium alloys, including titanium alloy composite parts. Because of the so large demand, the processing shop cannot use existing processing techniques to meet this demand. In order to increase production capacity, many processing plants will have to increase their production speed to speed up the processing of parts. If used properly, diamond tools and diamond coatings allow these plants to process titanium parts at higher speeds. 2. Drilling of composite materials Another application of diamond tools in the aerospace industry may surpass the theoretical "metal processing" because it involves composite materials, and parts made with such materials have begun to increase. Replace some metal parts. The use of diamond tools and other high-performance tools can greatly increase production efficiency. However, not every drilling process has the rigidity, stability, and low radial runout error necessary to get the diamond tool working properly. However, when diamond coated tools or PCD tools are applied to the drilling of composite materials, the increase in cost and productivity is also surprising. Because carbide carbide tools are fast in the processing of abrasive composites, the life of diamond tools is several times higher than the former. Its processing speed is so high that it can save a lot of time for each part that needs to be machined with many apertures. In fact, the same diamond tool can continue to drill certain metal materials, allowing diamond tools to efficiently process composite/aluminum alloy components or composite/titanium laminates. However, not every metal or material is suitable for making PCD, CBN or diamond coated tools. In addition to composite materials for aerospace applications, other suitable materials include titanium, aluminum and hard steel. Of course, the machine tools used must also be very suitable, because such tools require higher speeds. Machines with lower speeds may not be able to exploit the potential of such tools. At the same time, there is a certain requirement for the rigidity of the machine tool, although its rigidity requirements are not as high as many people think. In recent years, the toughness of these tool materials has been considerably improved. In addition, diamond tools and their associated tooling products are particularly suitable for long-term machining and high volume production. The reason is very simple, because the life of the tool is greatly improved. The tool's service life can be as long as this, so the shop can make the most of the tool's effective life for cutting.
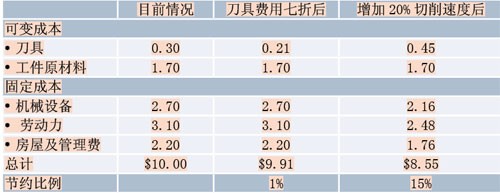
Figure 7 With modular tools, the shop does not need to set too many positions in the tool center of the machining center. How do users know if their shop has already made a profit? Mr. Graham said that a processing example of titanium in the aerospace industry can Give us some inspiration. Simply put, it can be compared with the needs faced by the workshop to see where the production capacity of the workshop is limited. In the process of machining parts, you must be able to adapt to more ordering requirements or achieve higher throughput. By increasing the speed, you can achieve these productivity targets with CBN and PCD tools without having to purchase new machines. .
Grassland Fence
Grassland Fence,Green Mesh Fencing,Galvanized Grassland Fence
Mesh Fence,Temporary Fence,Gabion Box Co., Ltd. , http://www.nsfence.com