Editor's Note: This article is based on the speeches of the three executive directors (expansion) meeting of the 4th Superhard Materials Branch held by Professor Kang Renke of Dalian University of Technology in Shenzhen. Precision cutting processing is one of the main processing processes for the preparation of semiconductor and optoelectronic crystal substrates, and it holds a high position in the manufacturing process of microelectronics and optoelectronic devices. With the rapid development of microelectronics and optoelectronics, higher requirements are placed on the cutting of semiconductors and optoelectronic crystals. High efficiency, low cost, high precision, narrow slit, small warpage deformation, low surface damage, low fragmentation rate, no environmental pollution, etc. are the new trends in the cutting process of semiconductor and optoelectronic crystals. Now, hard and brittle crystal material cutting methods include diamond circular saw cutting, band saw cutting, and wire saw cutting. Diamond circular saws are divided into diamond outer circle and diamond inner circular saw; band saw is divided into steel belt, diamond band saw and steel saw; wire saw is divided into wire saw, diamond bead saw, diamond wire saw Three kinds. Diamond outer circular saw cutting technology Diamond outer circular saw cutting technology is an early cutting method. The diameter of the circular saw blade for electroplating diamond on the outer circumference is about 200mm, and the maximum is up to 400mm. It is mainly used for cutting, grooving, etc. of materials such as gemstones, quartz, ferrite, and ceramics. The advantages are: simple structure, easy operation, and cheap blade; the disadvantages are: thicker blade, wide kerf, large material loss, poor parallelism of the cutting surface, and only small diameter or thin workpiece. A typical application of a diamond outer circular saw is to cut a silicon wafer into separate chips in IC fabrication. Diamond internal circular saw ( ID ) cutting technology
Diamond internal circular saw (ID) cutting technology diagram The advantages of diamond internal circular saw cutting technology are: 1. Good rigidity, can be made very thin, reaching 0.1mm; 2. High cutting precision, the thickness difference of the diameter of 200mm wafer is only 0.01 Mm; 3. The equipment is cheap, the price of the cutting machine used is only 1/3 of the price of other cutting tools. 14; 4. Each piece can be adjusted radially and slice thickness; 5. Small batch size Flexible adjustment during processing. Disadvantages are: 1. The surface damage layer of the slice is large; 2. The knife edge is wide, the material loss is large; 3. The productivity is low, only one piece is cut at a time; 4. Only the straight line can be cut, the surface cannot be cut; 5. The cutting diameter can only be smaller than 200mm wafer. The band saw cutting diamond band saw is a circular saw blade with the theme of electroplated diamond abrasive or inlaid diamond agglomerate. The band saw appeared in the 1950s, and it was only developed in China in the 1980s. The advantages are: fast sawing speed, low tool material consumption and low noise. The disadvantages are: large kerf, low cutting precision, regular requirements for blocks, and no multi-piece cutting. Wire saw wire saws are classified into four types according to the use of abrasive grains: wire saws using free abrasives, wire saws using consolidated diamond abrasives, wire saws brazed with diamond beads, and wire saws without abrasives. Free abrasive grain multi-line cutting
Free abrasive grain multi-wire cutting diagram Free abrasive grain multi-wire cutting is to use a wire wrapped around a set of wire guide rollers to form a row of cutting lines arranged at regular intervals. The wire moves in a certain direction and will contain silicon carbide, etc. The cutting fluid of the free abrasive is brought to the workpiece to cut the workpiece under a certain pressure to form a slit. The DS262 wire saw developed by meyar+burger for cutting solar wafers has the ability to simultaneously cut four 520mm long and 153×153mm silicon rods. The DS262 wire saw has a set of slices up to 4,400 pieces, which is equivalent to 50 pieces of day machine workload or 50 days of high quality slicer. The advantages of free abrasive multi-line cutting are: 1. The sheet thickness consistency is good, the slice thickness is guaranteed by the precision of the wire reel; 2. The raw material is saved, the slit is narrow, and the wire saw diameter is 0.08mm - 0.18mm, The inner circular saw blade has a blade width of 0.3mm-0.38mm; 3. can cut large-size crystals; 4. large slice size; 5. thin slice, uniformity of wire saw, less interference factors, stable cutting process; The residual stress and deflection of the slice are small, and the surface and subsurface damage layers are small. Disadvantages are: 1. It is difficult to adjust the thickness of the slice; 2. It is not suitable for small batch production; 3. The use cost is high, the steel wire and the reel are worn at the same time, and the service life is short; 4. Maintenance is difficult. Consolidated diamond abrasive wire saw
Consolidation of several diamond abrasive wire saw diamond wire saw cut in the form of a single line is divided into a reciprocating diamond wire saw endless diamond wire saw and a rotary diamond wire saw; multiple wire cutting of diamond wire saw into a reciprocating diamond wire saw. The toroidal rotary wire saw is welded into a ring shape and can be cyclically cut by a guide wheel. Advantages: 1. The entire length of the wire can participate in cutting; 2. Long service life; 3. High cutting speed (up to 10-20m/s). Disadvantages: A wire saw must first cut a lead groove when cutting the inner surface. The advantages of the single-line reciprocating diamond wire saw cutting machine are: simple structure, good adaptability, and cutting processing of the inner and outer surfaces; the cutting direction and the tilting angle can be freely changed to perform accurate complex contour cutting. The disadvantage is that the effective working strength of the wire is limited, the wire utilization rate is not high, and the cutting speed is low (generally 2-3 m/s). The advantages of multi-line reciprocating diamond cutting are: 1. It can carry out large-size workpiece slicing; 2. It can cut multiple pieces at the same time, and the output is high; 3. It can cut precision narrow slits, it is suitable for cutting precious materials, and the cutting diameter is only better than the sawing wire. The diameter is 0.01-0.015mm; 4. The brittle soft material is cut to ensure that the edge is not damaged; 5. The temperature is low when cutting, the slice is processed and the layer is shallow, which can be used to cut the fragile material; the wire saw has a long service life; 6. Environmental pollution small. Material removal mechanism for free abrasive and bonded abrasive wire saw cutting. Free abrasive wire saw cutting mechanism: three-body friction and wear, rolling embedding of free abrasive, similar to grinding. The mechanism of the fixed abrasive wire saw cutting: two-body friction and wear, the ploughing effect of the abrasive grain, similar to the grinding of the fine grinding wheel. In the case where the cutting depth of a single abrasive grain is sufficiently small, shaping of the shaping zone can be achieved.
Schematic diagram of material removal mechanism of free abrasive and fixed abrasive wire saw cutting. Preparation technology of diamond wire saw The consolidation method of diamond abrasive in diamond wire saw has rolling embedded, extrusion or stamping method, metal bond consolidation (brazing) ), metal bond consolidation (electroplating), resin bond consolidation. Rolling embedding method This method directly inserts the super-hard abrasive into the steel wire collective by mechanical action rolling. U.S. Patent 4,485,757 has proposed a process for preparing a continuous diamond wire saw by rolling embedding, and the diamond prepared by the process. The diamond coating of the wire saw has a uniform diameter and uneven thickness and wire diameter, and it is difficult to produce a diamond wire longer than 120 meters. Moreover, the superabrasive is rolled into the steel wire base by mechanical action, and the strength of the steel wire is greatly reduced. Extrusion or stamping method This method is to squeeze the diamond particles into the surface of the steel wire by two or more punching extrusion die, and then apply a layer on the surface of the diamond wire formed by extrusion. 1-10 μm metal, non-metallic materials. The advantage of this method is that an automated production line can be formed, and a continuous diamond wire having a length of more than 60 kilometers, a uniform diameter, and good abrasion resistance can be prepared, and the production cost is low. The disadvantages of this method are the same for rolling, as the diamond particles are directly stamped into the wire surface, which greatly reduces the strength of the wire.
Extrusion or Stamping Method Schematic Resin Bonding Diamond Wire Saw At present, the wire diameter of resin bond diamond wire saw is less than 0.2mm. Since the process temperature is much lower than that of brazing, the wire will not be deformed due to high temperature and cause tensile strength. Attenuation is a great help for reducing the wire diameter. Although the resin's holding power for diamond abrasives is not as good as that of hard soldering, it has the advantages of low process cost, small wire diameter and low consumables. Manufacturing Process of Resin Bonding Diamond Wire Saw - Thermosetting Resin Consolidation Method For Resin Bonding Diamond Wire Saw Manufacturing Process - Thermosetting Resin Consolidation Method, Sumitomo Electric Industries Co., Ltd. and Osaka Diamond Industry Co., Ltd., Osaka Prefecture, Japan A patent jointly filed by Shanggang Yongfu et al., the wire saw is characterized by adhesive fixed abrasive grains and filler on the high-strength core wire, and the abrasive size is not less than two-thirds of the thickness of the resin bonding layer, and the filler Two-thirds of the thickness of the small rain adhesive. The curing of the resin in the wire saw manufacturing requires a heating and sintering process, so the wire saw manufacturing speed can only be increased to about ten meters per minute.
Resin bond diamond wire saw manufacturing process - photocurable resin consolidation method To reduce the manufacturing cost of the resin bond diamond wire saw , that is, to increase the production speed, Japan's Ben Junzhi et al. have developed a fast curing UV curing resin. Methods. When the binder is made of an ultraviolet curing resin, the adhesion strength between the abrasive layer and the core wire is low, and the abrasion resistance of the wire saw is remarkably lowered, but a double-layer grinding with an ultraviolet curing adhesive layer between the core wire and the abrasive grain layer is used. After the grain structure, the wear resistance of the wire saw is improved. In order to further improve the abrasion resistance and the torsional strength of the wire saw, the alumina powder is added to the bonding agent, and the obtained wire saw can increase the speed of the wire saw by more than 10 times compared with the conventional thermosetting wire saw. Studies have shown that the larger the size of the resin bond diamond wire saw abrasive, the faster the cutting speed, but the cutting speed varies greatly with time. At the same time, all the resin bond diamond wire saws have the characteristics of low abrasive holding strength, poor heat resistance, low wear resistance and serious wear of the wire saw during processing. Electroplated Diamond Wire Saw Composite Plating Technology The composite plating technology is a composite coating formed by metal electrochemical methods, in which one or several insoluble solid particles are uniformly mixed into a metal plating layer. This method of preparing a composite coating is called composite plating. This technology also has some other names abroad. For example, dispersion plating, inlaid plating, dispersion plating, and combination plating, and the like. The super-hard material composite plating process uses a super-hard material as a dispersed particle, and a metal plating layer formed with a metal is called a super-hard material composite plating layer. Composite plating of superhard materials is not done in one step. For most superhard material electroplating products, it generally includes several steps of pre-plating, sand-plating, thickness and bright plating. The super-hard material composite coating structure is more complicated than the general composite coating, including the bottom plating layer, the upper sand plating layer, the thick plating layer and the bright plating layer.
Plating Plating Structure Drawing Electroplating Diamond Wire Saw Base Material Selection and Plating Process The common process flow for steel substrate nickel plating or nickel-cobalt alloy plating process is as follows:
The choice of plating solution nickel plating solution can be divided into: ammonia oxide type, watt type, sulfamic acid type and chloride type. The watt type plating solution has the advantages of simple composition, stable plating solution, easy operation and maintenance, and good corrosion resistance. Add some additives to the solution to the bright or semi-bright coating. It is currently the most widely used nickel plating solution. The ammonia sulfonic acid type can adopt a high current density, has a high plating rate, a high deposition rate, a low internal stress, a good dispersing ability of the plating solution, and a simple, stable and easy to manage plating composition. Sanding method for electroplated diamond wire saw Upper sand refers to a plating process after the pre-plating step, the purpose of which is to initially adhere a layer of abrasive particles immediately adjacent to the surface of the substrate to the low-plated layer by electrodeposition of metal. The sanding method includes a suspension method, a sand burying method, and a mosaic method. Suspension method micro-powder composite electrodeposition suspension method is to put a certain amount of micro-powder abrasive grains into the plating solution, and use the means of stirring, shaking or aqueduct transmission to suspend the abrasive particles in a dispersion state in the plating solution, while electroplating, fine powder The abrasive grains are simultaneously deposited as the metal ions are reduced, thereby forming a composite plating layer. The process of co-deposition of particles and metals is generally divided into the following three stages: 1. The suspended particles in the plating solution move toward the vicinity of the cathode surface; 2. The particles adhere to the surface of the cathode by the force between the electrodes and stay for a certain period of time to ensure A part of the particles is buried in the plating layer; 3. The particles are buried in the plating layer by the metal deposited on the cathode. The composite coating obtained by the sand-embedded composite electrodeposition method has diamond particles deposited on each surface of the circumference of the wire, and the surface area percentage is about 40-50%. The comprehensive distribution of the diamond particles on the surface of the wire is obviously better than the suspension. The composite coating obtained by the method. Electroplated diamond wire surface Abrasive height Exposed height Electroplated diamond wire surface Abrasive height is also the diamond abrasive grain embedding rate, and the ratio of the depth of diamond particles embedded in the coating to its diameter, it is an important control of electroplated diamond wire saw aims. It has a large impression on the cutting force, cutting rate, wire saw life and so on of the electroplated diamond wire saw. The exposed height of the abrasive grain on the surface of the electroplated diamond wire is usually controlled at 70% to 90%. The diameter of the diamond particles is up to the upper limit and the diameter is small. The exposed height of the diamond abrasive grains mainly depends on the particle size of the abrasive grains, the plating time and the current efficiency, and the location and direction of the diamond abrasive grains in the plating layer are also affected. Table 2 Relationship between sanding time, thickening time and diamond particle size
The continuous diamond wire sawing test of the diamond wire has a diamond abrasive grain content of about 50% in the composite coating, and the abrasive grain coverage has basically reached more than 60% of the abrasive grain size. Performance Evaluation of Electroplated Diamond Wire Saws The following two aspects should be considered for the performance inspection of diamond wire saws: one is the inspection of the surface plating of the electroplated diamond wire saw, including the quality inspection of the plating appearance, the geometrical inspection of the wire saw, and the consolidation of the diamond abrasive grains. Strength check. The second is the detection of the mechanical and mechanical properties of the electroplated diamond wire saw, including tensile strength characteristics and elongation, fracture torsion characteristics, bending properties and the like. High-speed electroplating process of diamond wire saw Japan's Chiba Kangya and others developed a super-high-speed electroplating process using a felt brush to develop a high-speed electroplating production method for diamond wire cutting tools. In this method, the sulfa nickel plating solution is used, and the core wire is plated while the felt brush is rotated, and the coating with excellent adhesion can be obtained, and the production speed can reach 33 μm/min, which is 30 times faster than the ordinary plating method, and is greatly reduced. The production cost not only improves the production speed of the wire saw, but also improves the processing efficiency and service life of the wire saw.
Stranded diamond wire saw Japanese Ishikawa Kenichi et al. researched and developed a new type of diamond wire saw with a stranded wire, as shown below
Composite Electrospray Plating of Diamond Wire Saws Shenyang Jingtong Diamond Composites Co., Ltd. Jiang Xiaoping applied for a composite electrospray plating method to prepare diamond wire saws. Diamonds were drilled on stainless steel wires with a diameter between 0.1 and 1 mm. The electrospray of the particles increases the speed of production. The disadvantage of this method is that the tool production time is too long in the electroplating process, and the tool manufacturing cost is also high. The research progress of diamond wire saws entered the 20th century, especially in recent years, the demand for consolidated diamond wire saws has increased dramatically, and the diamond wire saw cutting technology has also developed rapidly, and the research on its preparation and application has gradually deepened. Mainly concentrated in the following aspects: 1. Diamond wire saw cutting mechanism; 2. Diamond wire saw performance and aging mechanism; 3. Wire saw high-speed cutting technology; 4. Ultrasonic vibration-assisted diamond wire saw cutting; 5. Cutting force measurement And constant force testing. The new trend is the study of new structural diamond wire saws and diamond abrasive grain consolidation techniques. Electroplated diamond wire saw market situation Electroplated diamond wire saw technology status and research direction Electroplated diamond wire saw production technology is very mature abroad, and applied for a number of production patents. Domestic research on the production technology of electroplated diamond wire saws is still in its infancy, and the electroplated diamond wire saws used mainly rely on imports. Electroplated diamond wire saws have received great attention. Current research directions: 1. To study the substrate used for electroplated diamond wire saws, mainly steel wire substrates. There are few studies on other substrates, and the base materials are relatively simple, so further expand the electroplated diamond wire saws. The matrix has become one of the research directions. 2. Due to the unsatisfactory service life of the commonly used chainsaw diamond wire saws, further strengthening the bonding force of the bonding agent to diamond, and developing a more durable and durable diamond wire saw has become one of the research directions. 3. The currently used electroplating technology for preparing electroplated diamond wire saws takes a long time, further strengthening the research of electroplating technology, shortening the preparation cycle and reducing the manufacturing cost has become one of the research directions.
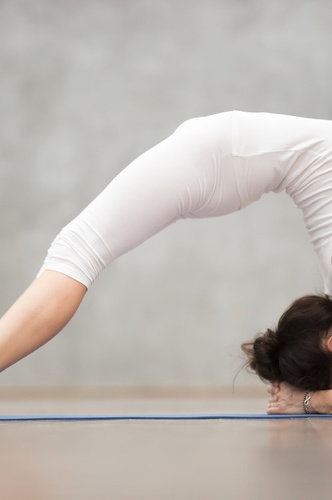
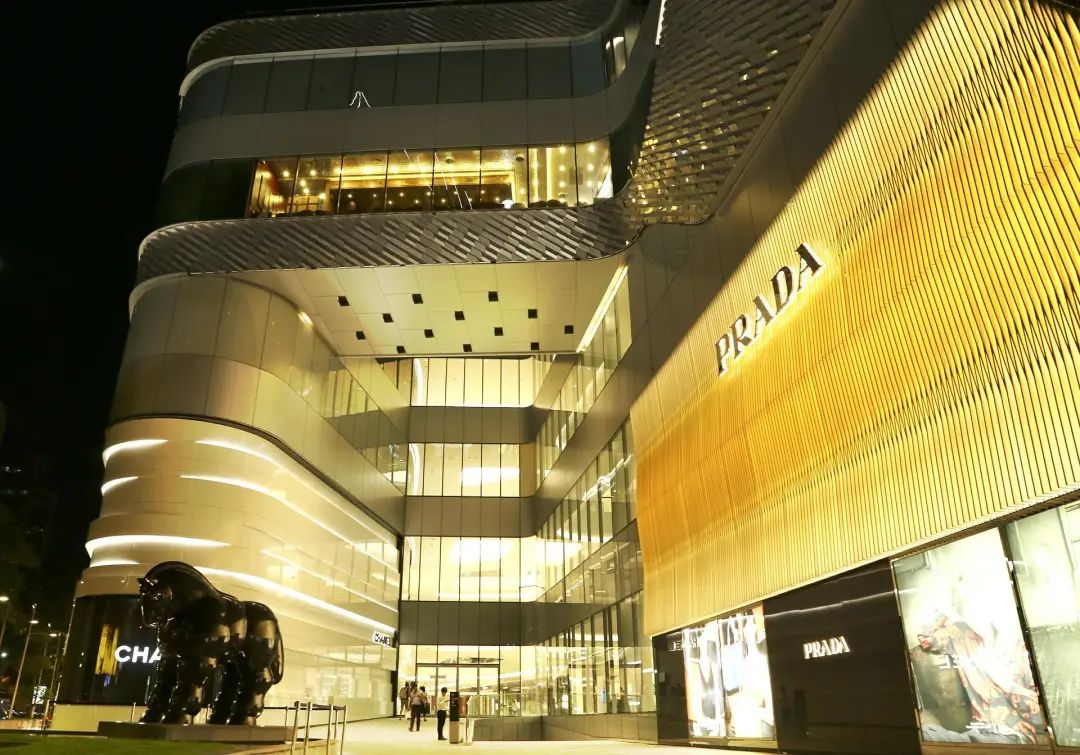
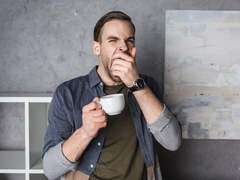
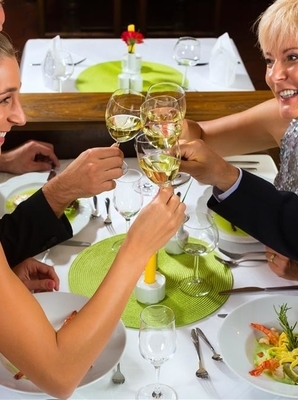
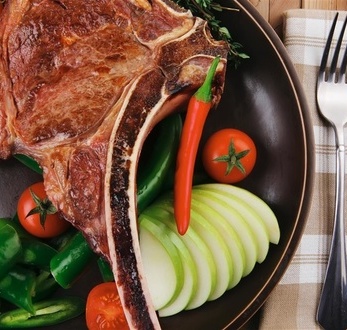
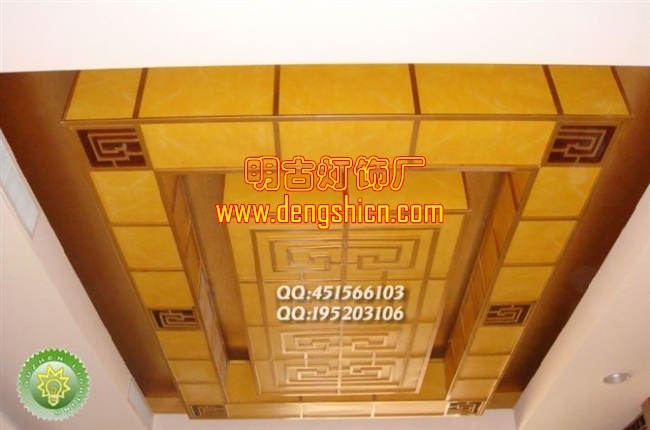
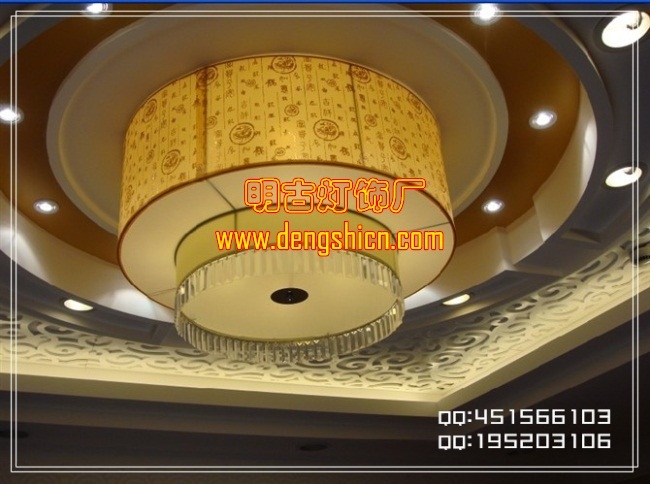
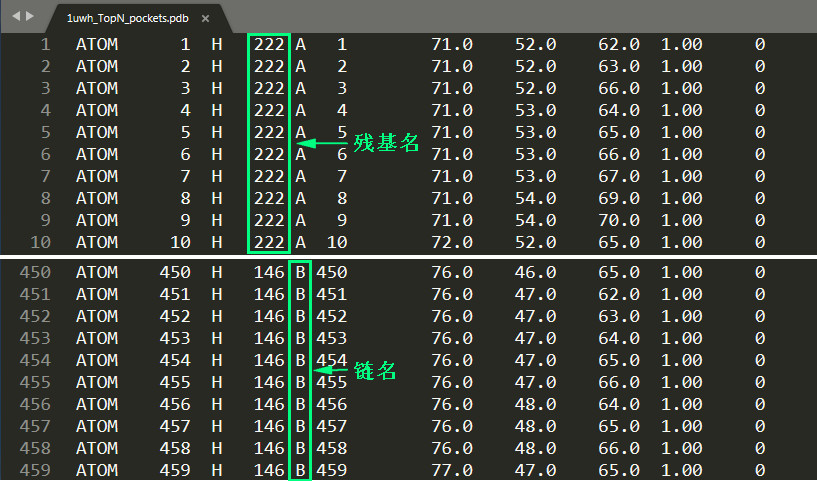

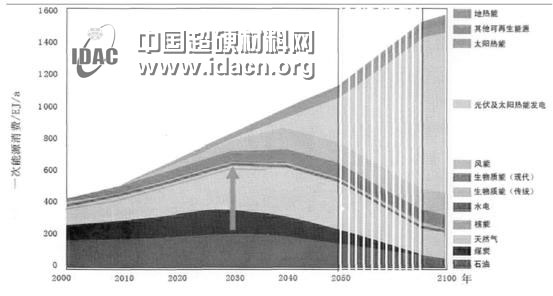
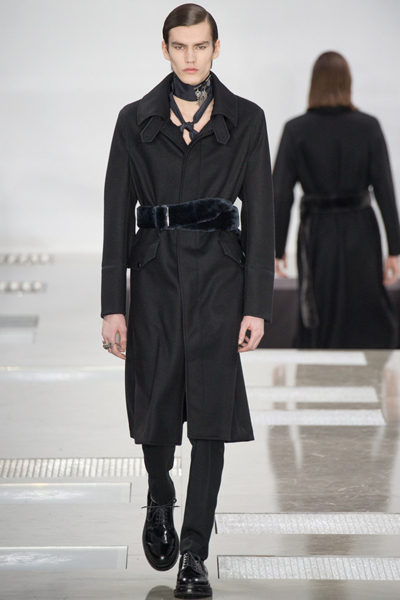
A laser band-pass filter has a wavelength of 355nm/532nm/633nm/1064nm/10.6 um and is characterized by high damage threshold, high surface quality and high precision.
Laser Bandpass Filter,Laser Aquarium Filter,Lidar Pass Band Filter,Bandpass Optical Filters
Changchun Champion Optics Co.,Ltd , https://www.champion-optics.com