A superhard material coated abrasive article refers to an abrasive article that adheres superhard material abrasive grains to a flexible flexible substrate with an adhesive.
Grinding is the largest part of the abrasive consumption of all processing methods. The increase in the output of diamonds and CBN provides a strong material support for accelerating the development of tools. The National Twelfth Five-Year Plan outlines once again that it is necessary to “build a resource-conserving and environment-friendly society†and urgently require industrial production to change the traditional extensive The type of processing has been transformed into an intensive processing method that is environmentally friendly and resource-saving.
Due to the influence of production equipment, raw material prices, manufacturing levels and other factors, the application of superhard material coated abrasives in China is rare. However, in industrialized countries, due to the emphasis on environmental protection, as well as the production technology base, and the full range of products, it has been applied in many fields, and some enterprises have already produced scale.
The world-famous abrasives companies, such as the US 3M, NORTON company's catalogue, have a large number of super-hard material abrasive products, from the polishing of the car body to the engine crankshaft, camshaft processing is to use high-grade super-hard materials sandpaper and poly Ester film belt and disc. Figure 1 is a 3M company superhard material coated abrasive.
"The 21st century is the century of diamonds" [1], the application of superhard materials is bound to expand, and superhard materials coated abrasives are one of the most promising and promising development directions. Flexible superhard materials such as abrasive belts made of diamond or CBN, flexible grinding wheels, and grinding discs will gradually replace the corundum and silicon carbide tools that are currently used in large quantities on the market.
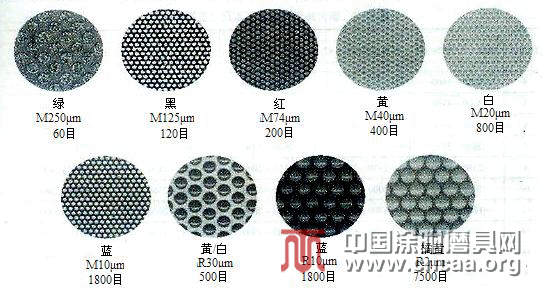
2 Classification of coated abrasives
According to the abrasive material, it can be divided into diamond and cubic boron nitride coated abrasives.
According to the processing method, it can be divided into electroplated and resin super hard material coated abrasives.
Resin super-hard material coated abrasives are further divided into coating type and dispensing type.
According to the use, it can be divided into abrasive belt, abrasive belt ring, flexible grinding wheel, grinding disc, polishing sheet and soft boring tool.
Diamond coated abrasives are used to process hard materials such as non-ferrous metals, glass, ceramics, and precious stones.
Cubic boron nitride coated abrasives are mainly used for steel parts, mainly cubic boron nitride belts for various belt grinding machines.
3 three major elements
The three main elements often involved in the manufacture of coated abrasives are the matrix, abrasives and binders. Improvements in any of these three elements will result in changes in the performance of the coated abrasive product.
The substrate is a carrier for the abrasive abrasive and binder and is the base material for grinding or polishing. The substrate is mainly divided into four types: paper base, cloth base, composite base and non-woven fabric.
The types of cloth materials are now cotton, hemp, rayon, synthetic fiber and polyester fiber. In the past decade or so, rayon and polyester fiber cloths have been vigorously developed in large-area strong grinding, and the latter, in particular, the use of it as a belt and other coated abrasive substrates is a trend.
The non-woven fabric is a wide-volume roll formed by separately or in combination of natural fibers and synthetic fibers into a fiber web by heating, pressing or bonding. It must be glued to a cloth or paper base to make a belt or a non-woven wheel.
It is worth noting that the use of polyester film substrates in foreign countries to manufacture super-hard material abrasive belts, abrasive sheets and polishing sheets has obvious advantages in grinding difficult-to-machine materials. It can be considered that with the polyester film as the substrate, the super-hard material coated abrasives will expand the application range and extend to the field of precision and ultra-precision grinding and polishing [2].
The non-woven fabric is a wide-volume roll formed by separately or in combination of natural fibers and synthetic fibers into a fiber web by heating, pressing or bonding. It must be glued to a cloth or paper base to make a belt or a non-woven wheel.
Abrasives are a granular material that acts as a grinding, grinding and polishing agent on a coated abrasive. Abrasives are generally classified into natural abrasives and artificial abrasives.
Natural abrasives include garnet, natural corundum, natural diamonds, and the like.
Artificial abrasives include corundum, silicon carbide, synthetic diamond, and cubic boron nitride.
The super-hard material coated abrasives are made of diamonds, which are optional MBD series diamonds for grinding and RVD varieties for polishing. The particle size is optional size of fine grinding and grinding: 50∕60, 60∕70, 80∕100, 100∕120, 120∕140, 140∕170, 170∕200, 200∕230∕270, 270∕ 325, 325 ∕ 400; superfine abrasives of optional micro-powder grades for polishing: W40, W20, W14, W10, W7, W5, W3.5, W2.5, W1.5, W1.0, W0.5 .
The binder acts as a bonding abrasive and a substrate to impart a certain shape and strength to the abrasive article. The binder in the coated abrasive is generally composed of a substrate treating agent, a primer, a size, and the like. The binders used for the coated abrasives are mainly animal glues and synthetic resins. Phenolic resin has high bonding strength, good water resistance, acid resistance and weather resistance, especially the use of water-soluble phenolic resin, making it one of the most important binders for coated abrasive products. Nano-SiO2 bisphenol phenolic resin binder can become the second major material for the production of coated abrasives. The binders used in the manufacture of coated abrasives in developed countries are becoming more and more specialized, and the binders used are different.
4 diamond belt application
The diamond abrasive belt is divided into a metal bond and a resin bond diamond abrasive belt according to different binders. In the western industrialized countries, there are several companies with more complete types, including different sizes and sizes, and different working layer colors to distinguish the particle size. Table 1 is a diamond belt product with different surface shapes of a Swiss company. 3].
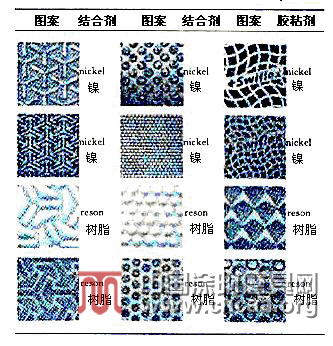
4.1 Diamond belt for automotive glass edging
The glass edging mainly adopts two methods: abrasive belt edging and grinding wheel edging. Abrasive belt grinding has relatively low equipment requirements, small glass damage, and can be used for profiled glass processing, especially for automotive glass processing, but has an unmatched service life.
Because diamond abrasive belts have an irreplaceable advantage in glass edging, most foreign manufacturers use diamond abrasive belts as automotive glass edging tools. However, due to the immature diamond belt and equipment technology in China, the imported diamond belt and equipment are expensive, which leads many manufacturers to use SiC belt for edging.
The silicon carbide abrasive belt is used for glass edging. Due to its short service life and frequent replacement, the processing efficiency is low and the surface quality is poor, which is extremely disadvantageous in the production of continuous glass production lines. With the diamond belt, the number of replacements per belt is increased from less than 30 min/time to 72 hours/time, which greatly improves the working efficiency of the overall production line. Table 2 compares the cost of use of diamond abrasive belts and silicon carbide abrasive belts.
Table 2 Comparison of the costs associated with the production of 550,000 m2 automotive glass using different types of edging abrasive belts
Belt type | Unit price (å…ƒ ∕ æ¡) | Time (days) | Number of tools (bar) | tool cost (ten thousand yuan) | Artificial water and electricity consumption (ten thousand yuan) * | Total related costs (ten thousand yuan) | Related unit cost (yuan ∕ m 2 ) | Edging quality |
Silicon carbide belt | 10 | 979 | 94000 | 94 | 2575 | 2669 | 48.5 | difference |
Diamond belt | 2500 | 365 | 230 | 57 | 960 | 1017 | 18.5 | it is good |
It can be seen from Table 2 that although the diamond belt is expensive to manufacture, the unit price is much higher than that of the silicon carbide belt. However, due to the short service life and high replacement frequency of the silicon carbide belt, the actual cost of the tool and the cost per unit of cost are far high. In the diamond belt. Therefore, the diamond abrasive belt has an incomparable cost performance advantage in the production of automotive glass edging, and is a new generation of energy-saving and environmentally-friendly high-performance products.
In 2010, China's automobile glass consumption exceeded 80 million m2, and in recent years, it has increased by more than 20% every year. Table 3 is the estimated demand for domestic automotive glass edging diamond belt.
Table 3 Domestic automobile glass edging diamond belt demand calculation table
Annual auto glass Processing capacity (million m 2 ) | Glass edging Bus length (100 million m ) | Grinding each pair of belts Line length (million m ) | Annual belt Consumption (bar) | Annual belt demand |
8000 | 3.4 | 2 | 34000 | 8500 |
4.2 Roll wear coating processing
Corrugated roller is a key component in the corrugated board production line. Its sturdy shape and manufacturing precision, wear resistance, service life and running speed are the main technical indicators to measure its quality and economy. It directly relates to the product quality and economy of the enterprise. benefit.
In order to improve the wear resistance and surface hardness of the corrugating roller and meet the needs of the development of the corrugated board production line in the direction of high speed, it is often necessary to apply a layer of WC-Co cermet coating on the surface of the corrugating roller by using advanced thermal spraying technology.
Generally, the coating thickness is 250 μm, the surface roughness Ra of the coating after spraying is 8 μm, and the Rt (maximum profile unevenness) is 70 μm. Therefore, it is generally necessary to remove the surface layer of about 100 μm to achieve the required precision and smoothness. First use 200# diamond abrasive belt to remove 70-75μm. However, due to the high price of diamond abrasive belt, in order to reduce the processing cost, the current process also uses grinding wheel grinding; the remaining 25~30μm must be used for grinding with 400# diamond sand. The grinding equipment used is referred to abroad as a "diamond film ultra-precision grinding machine".
4.3 Surface grinding and chamfering of silicon ingots
In order to improve the grinding efficiency and reduce the surface damage of the silicon ingot during grinding, the use of diamond abrasive belt is undoubtedly the best choice. The use of diamond abrasive belts requires only one size to complete all processes, and has the following significant advantages: reduced number of processes, short processing time; improved surface roughness, improved yield; reduced labor costs; easy to maintain. In addition to the surface grinding of silicon ingots, diamond abrasive belts can also be used for chamfering silicon ingots.
5 CBN abrasive belt application
The use of CBN abrasive belt has superior performance and cost performance advantages:
5.1 Grinding of precision bearings
After the precision bearing is formed, the surface is ground and polished, and it is often necessary to use a belt. However, due to the high precision of the shape and surface finish of the finished product, the ordinary abrasive belt is used, the surface conformability is poor, the abrasive is easy to be smashed, the swarf is easy to accumulate after smelting, the surface quality is damaged, and the life of the belt is low, which requires frequent Replacement, low processing efficiency. The use of CBN abrasive belt, the shape retention of the abrasive is good, the service life of the abrasive belt is long, the time for stopping the belt change is reduced, the productivity is greatly improved, and the comprehensive performance is better [4].
5.2 CNC belt grinding machine
For a long time, CNC abrasive belt grinding machines use ordinary abrasive belts as grinding tools. Even with high-hardness abrasive belts such as zirconium corundum and ceramic abrasives, the service life is still very low. The belt needs to be replaced frequently, which greatly reduces the numerical control grinding machine. Use efficiency. With the gradual maturity of CBN abrasive belt technology, CBN abrasive belts are used in CNC grinding machines, which will gradually replace ordinary abrasive belts with their extraordinary service life, good processing efficiency and processing quality.
6 other super hard materials coated abrasives
Other superhard material coated abrasives mainly include diamond abrasive sheets, diamond hand grinding blocks, diamond abrasive brushes and the like.
7 Conclusions and prospects
7.1 With the continuous development of modern machining and the emergence of various new materials, the requirements for machining accuracy and surface roughness are getting higher and higher, and the corresponding advanced grinding technology and abrasive tools, especially coated abrasives. Towards higher efficiency, longer life and ultra-precision.
7.2 Coated abrasives have an irreplaceable advantage in the surface grinding and polishing of large-size, profiled surfaces, brittle and fragile workpieces.
7.3 Ordinary abrasive coated abrasives processing efficiency, processing surface quality is not as good as super-hard materials coated abrasives, making super-hard material coated abrasives have a special place in special occasions such as high precision, high life and automatic production lines. It can be predicted that the super-hard material grinding tools will have a huge development space, and the prospects are beautiful!
7.4 China is a superpower in the world of superhard material production. Our raw materials, complete varieties and low value are our advantages [5].
7.5 For a long time, everyone has a misunderstanding that ordinary abrasive coated abrasives are cheap and the processing cost is low, while superhard materials coated abrasives are expensive and costly to use. In fact, in many cases, due to superhardness The material coated abrasive has a long service life, and the processing efficiency is much higher than that of the ordinary coated abrasive tool, and the tool replacement time is saved, the comprehensive processing efficiency is greatly improved, the comprehensive processing cost is reduced, and the material processing quality is greatly improved. Therefore, the super-hard material coated abrasive has better comprehensive processing performance and cost performance advantages. Get out of the misunderstanding as soon as possible, how many things, has been anxious, 10,000 years is too long, just fight for the day!
7.6 After decades of development, abrasive belt grinding technology has entered a new stage of modernization. Of particular note is the successful application of superhard material abrasive belts, which show unique advantages in grinding difficult-to-machine materials, from workpiece grinding for general precision requirements to high-precision, ultra-high precision parts. Grinding, such as grinding, polishing of precision parts such as magnetic disks, magnetic heads, video recorders, copiers and optical fiber guides.
7.7 In recent years, China's automobile industry and machinery manufacturing industry have flourished. It is reasonable to use a large number of super-hard materials to coat abrasives, which has a large domestic demand space. However, all domestic auto companies, such as Volkswagen, Citroen, GM, Buick, Toyota, Honda, etc., use imported coated abrasives, mainly imported 3M company's coated abrasive products. Hugh! [6]
7.8 At present, 3M companies in the United States, Saint Gobain/Norton, Klingspor and other internationally renowned companies have a wide range of superhard materials coated abrasive products, which represent the world's superhard material coating grinding. With the highest level of research and manufacturing. When China can catch up, there should be a timetable.
7.9 According to the characteristics of small hard material sand belt with small size and high dimensional accuracy, the equipment should be miniaturized and automated. Including gluing machine, electrostatic sanding machine, laminating machine, flexing machine, slitting machine and dispensing machine.
references
1Wang Guangzu, Wang Wei, Talking about the 21st Century is the Chinese Diamond Century [J] Superhard Materials Engineering, 2010.1
2 Zheng Chao Lu Zhi, Development Status of Superhard Material Coated Abrasives [C] Proceedings of the 5th Zhengzhou International Superhard Materials and Products Symposium, 2008.9: 202~208.
3 Xie Zhigang, Liu Zhihuan, etc., application prospects and research status of superhard material coated abrasives (I) [J] Superhard Materials Engineering, 2011.2: 42~46.
4 Xie Zhigang, Liu Zhihuan, etc., application prospects and research status of superhard material coated abrasives (below) [J] Superhard Materials Engineering, 2011.3: 37~41.
5 An Jianmin, Wang Guangzu, the brilliance of the combination of “hard†and “soft†in the super-hard material belt [C] Proceedings of the Strait Cross-Strait Superhard Materials Technology Development Forum, 2010.10: 275-278.
6 Lv Zhi Zheng Chao, etc., design and manufacture of superhard materials tools [M] Metallurgical Industry Press, 2010, 204 ~ 222.
Intergrated Led Emergency Modules
The Intergrated Led Emergency Modules is match the compact LED fittings to improve the emergency function. Normally it is workable for small wattage from 3-60W LED panels, downlights, led tubes, tri-proof ceilings. Full power output or half power emergency output is optional. Customized emergency lighting time is available. Automatic lighting up when main power failures. Widely using for home, parking lot, office, building, warehouse, school, hospital, workshop etc.
Emergency Light Module,Emergency Led Flasher Module,Led Emergency Modules,Intergrated Led,led light with emergency battery
Foshan Nai An Lighting Electric Co.,ltd , https://www.naipslighting.com